Introduction: Why Fall Protection Compliance Matters in Nashville
Fall protection compliance is a crucial element for any business operating in Nashville’s construction and industrial sectors. The city’s ongoing growth fuels a surge in new builds, renovations, and infrastructure projects, each carrying inherent risks when employees work at heights. Without effective fall protection measures, companies expose their workers to preventable injuries, often resulting in long-term physical harm that can deeply impact families and communities.
Beyond the human cost, fall protection compliance in Nashville directly influences a company’s operational resilience. Incidents from inadequate fall protection can halt projects, trigger investigations, and lead to substantial fines, draining resources that could otherwise support business growth. Maintaining compliance demonstrates a company’s commitment to following OSHA and Tennessee state guidelines while positioning it as a reliable partner for clients, contractors, and employees.
By prioritizing fall protection, Nashville businesses establish a culture of care and accountability that extends beyond the job site. It signals to workers that their safety is valued, leading to higher morale, better retention, and a proactive safety mindset that reduces incidents across all aspects of operations. In a competitive market, businesses that embed fall protection into their safety programs gain a tangible advantage while upholding their duty to protect every individual on their team.
Understanding OSHA’s Fall Protection Standards
OSHA’s fall protection standards form the regulatory backbone for safeguarding workers at height, requiring comprehensive safety measures when employees work at elevations of six feet or more in construction settings. These standards outline the use of guardrails, personal fall arrest systems, and safety nets as critical elements of a robust fall protection strategy. Understanding these requirements is vital for Nashville employers who must align site operations with federal regulations to mitigate risks associated with working at height.
Employers bear the responsibility of ensuring fall protection systems are not only present but also effectively implemented on each job site. This includes conducting site assessments to identify fall hazards unique to the environment, selecting appropriate fall protection systems, and maintaining their integrity through regular inspections. The process goes beyond simply checking boxes; it demands a structured approach to risk management and the application of the most suitable fall protection measures for each specific task or site condition.
Equally important is the obligation to train workers in fall protection use, hazard awareness, and emergency response. OSHA’s guidelines require that employers provide clear, practical training to workers, ensuring they understand how to properly use fall protection equipment and identify unsafe conditions. For Nashville businesses, adhering to these standards means fostering a workforce that is both informed and empowered, significantly reducing the likelihood of falls while maintaining compliance during project execution.
Nashville-Specific Requirements You Need to Know
Fall protection compliance in Nashville involves more than meeting federal OSHA standards; it also requires navigating Tennessee Occupational Safety and Health Administration (TOSHA) guidelines and local codes that may influence project safety protocols. Nashville’s growth brings with it varied construction environments, from high-rise projects downtown to industrial maintenance on the outskirts, each with specific site conditions requiring tailored fall protection measures. Businesses that stay informed on Nashville’s regional compliance landscape can prevent fines and project delays that often arise from overlooked local regulations.
TOSHA occasionally enforces stricter inspection practices than federal OSHA, emphasizing detailed documentation and consistent fall protection training across all operational levels. Companies working on municipal or state-funded projects may encounter unique stipulations tied to contracts, requiring precise reporting and adherence to Nashville’s safety ordinances. Engaging in fall protection compliance at the local level allows businesses to build a strong working relationship with inspectors and demonstrate a proactive approach to workforce safety.
Beyond legal obligations, understanding Nashville-specific requirements for fall protection can significantly reduce operational risk. Variations in weather conditions, from heavy summer humidity to sudden winter ice, create additional fall hazards on site that must be addressed in safety planning. By embedding Nashville-focused compliance strategies into fall protection programs, companies enhance their resilience and maintain continuous productivity while demonstrating a commitment to protecting their employees.
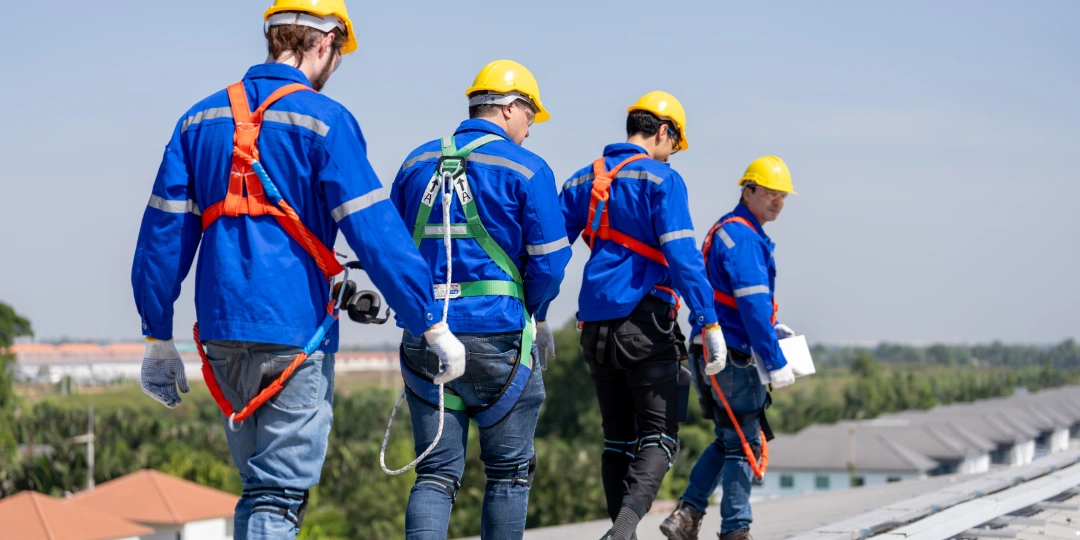
Common Fall Hazards on Tennessee Job Sites
Effective fall protection requires identifying and addressing common fall hazards that frequently appear across Tennessee’s diverse job sites. Slips on wet surfaces during humid Nashville summers, icy scaffolding in winter, unguarded roof edges, and unsecured floor openings are persistent challenges that contribute to fall-related injuries. Workers performing tasks on ladders or scaffolding without proper fall protection are especially at risk, often due to rushed project timelines or improper site planning.
Construction and industrial sites across Nashville often involve multi-level operations where open-sided platforms or incomplete stairways expose workers to serious fall hazards. Misuse or lack of personal fall arrest systems further increases risks, especially when workers are not adequately trained to recognize when and how fall protection should be used. By closely analyzing site conditions, businesses can anticipate these hazards and implement tailored fall protection measures to prevent incidents before they occur.
Addressing these common hazards requires a structured approach to fall protection that includes hazard recognition, implementation of guardrails or safety nets where applicable, and consistent use of personal protective equipment (PPE). Businesses in Nashville that incorporate hazard-specific training and proactive inspections into their fall protection plans build safer job sites, foster worker confidence, and reduce the operational disruptions that accompany fall incidents.
The Role of Fortier Loss Control in Fall Protection Compliance
Fortier Loss Control provides Nashville businesses with targeted support in achieving fall protection compliance, offering comprehensive site assessments that pinpoint specific vulnerabilities related to working at heights. Their experts conduct detailed evaluations that help businesses understand where their current fall protection measures align with OSHA and TOSHA standards and where gaps exist. This assessment-driven approach ensures that businesses address the unique risks present on each Nashville site, reducing the chance of regulatory infractions and incidents.
Beyond assessments, Fortier Loss Control offers tailored strategies for implementing fall protection systems that suit the workflow and structure of Nashville job sites. From recommending the right guardrail systems for high-rise construction to advising on anchor point installations for industrial maintenance, Fortier ensures fall protection plans are practical, effective, and compliant. Their partnership helps businesses align their safety protocols with evolving local and federal guidelines while maintaining operational efficiency.
Training is another critical area where Fortier Loss Control strengthens fall protection compliance. By providing on-site training sessions, instructional resources, and practical demonstrations, Fortier equips Nashville workers with the knowledge and skills necessary to utilize fall protection systems correctly. This integrated approach supports long-term safety culture development within organizations, positioning businesses to maintain consistent compliance while prioritizing the well-being of their employees.
Building a Site-Specific Fall Protection Plan
A robust fall protection program in Nashville begins with a site-specific plan that addresses the distinct hazards and operational flow of each project. Unlike generic safety outlines, a site-specific fall protection plan evaluates the layout, workflow, and height-related risks to establish clear, actionable strategies for worker safety. This plan should detail hazard identification processes, designate competent persons responsible for oversight, and document the methods and equipment used to implement fall protection on site.
The plan must also clearly outline rescue procedures in the event of a fall, including methods for prompt retrieval and medical response, ensuring compliance with OSHA’s requirement for immediate rescue planning. In Nashville, where projects range from busy urban construction to industrial facility maintenance, a site-specific fall protection plan should also account for variable weather conditions and localized site challenges that may increase fall risks. By tailoring the plan to the specific environment, businesses mitigate potential liabilities and enhance the protection of their workforce.
Worker involvement is critical in developing and executing a site-specific fall protection plan. Employees should be encouraged to provide input based on their observations and day-to-day experiences on site, promoting a shared responsibility for safety. This approach fosters a proactive safety culture, ensuring that fall protection measures are not only compliant on paper but also actively practiced, reducing the likelihood of incidents and reinforcing the organization’s commitment to safety.
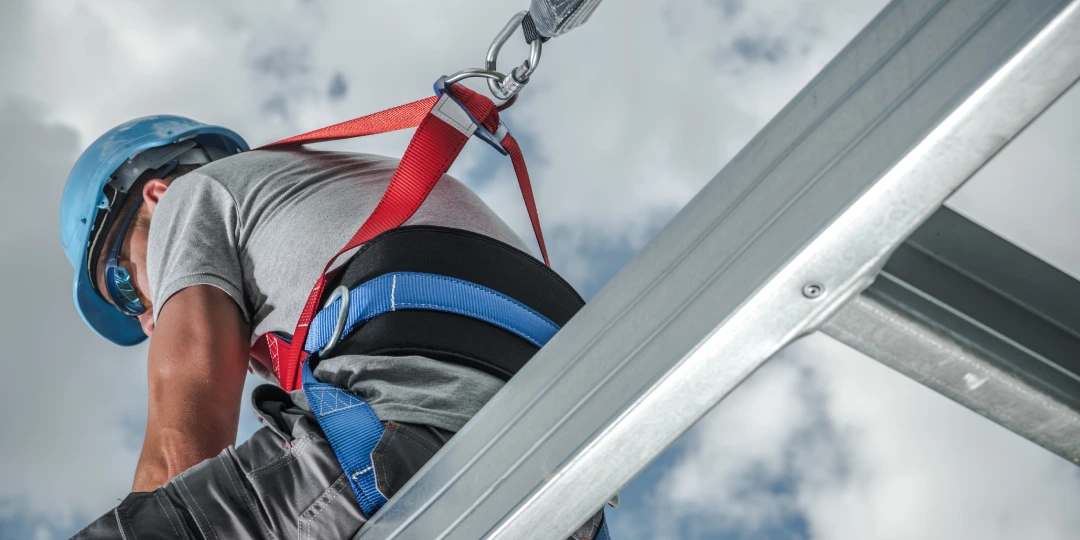
Key Equipment for Effective Fall Protection
Effective fall protection depends heavily on the correct selection and use of specialized equipment designed to prevent or arrest falls. Essential components include personal fall arrest systems such as full-body harnesses and shock-absorbing lanyards, which distribute arrest forces to minimize injury during a fall. Anchor points, chosen based on structural integrity and placement, are crucial in ensuring the reliability of the fall protection system, allowing workers to operate at height with confidence.
Guardrails and safety nets provide collective fall protection, reducing reliance on personal equipment and offering barriers that prevent falls from unprotected edges or elevated platforms. In Nashville’s busy construction sites, where workers may frequently transition between different levels, the use of guardrails on scaffolding and open-sided floors is vital for maintaining a secure environment. These systems should be installed according to OSHA specifications and routinely inspected to ensure their integrity is uncompromised by wear or site conditions.
Regular equipment inspections are essential in any fall protection program, as equipment degradation can occur from heavy use, exposure to the elements, and improper storage. Employers must develop a clear inspection schedule, with competent personnel checking harnesses, lanyards, anchor points, and guardrails for damage or wear. By maintaining the reliability of fall protection equipment, Nashville businesses not only protect their workforce but also reinforce a disciplined approach to compliance and operational excellence.
Training Workers for Fall Hazard Awareness
Training is the backbone of any successful Fall program, equipping workers with the knowledge and practical skills necessary to identify hazards and use protective equipment effectively. A well-designed training program should include comprehensive instruction on recognizing fall hazards unique to the job site, understanding the limitations of the equipment, and correctly donning and adjusting harnesses and lanyards. For Nashville’s workforce, training should also address site-specific risks influenced by weather conditions and site configurations.
Interactive training methods, including hands-on demonstrations and scenario-based exercises, enhance worker retention and confidence in using fall protection systems. Workers should be encouraged to actively participate in training sessions, ask questions, and practice using the equipment under supervision to ensure competence before exposure to height-related tasks. Regular refresher courses are necessary to reinforce safety practices, update workers on new equipment, and adapt protocols to evolving job site conditions.
Employers must document all training efforts to demonstrate compliance with OSHA and TOSHA requirements, providing clear evidence during audits or inspections that workers have received adequate fall protection instruction. More importantly, effective training fosters a safety-conscious culture, empowering workers to take ownership of their safety and that of their colleagues, resulting in a cohesive, vigilant team dedicated to maintaining fall protection standards on every Nashville project.
Navigating Incident Response and Reporting
Even with robust fall protection systems in place, incidents can occur, making a clear incident response plan a critical component of compliance and worker safety. A comprehensive fall protection incident response plan should include immediate first aid procedures, rapid communication with emergency services, and clear internal reporting lines to ensure timely medical intervention for affected workers. Quick and organized response can significantly reduce the severity of injuries, underscoring a company’s commitment to its workforce.
Incident reporting is a regulatory requirement under OSHA and TOSHA guidelines, necessitating prompt documentation and submission of incident details within the stipulated timelines. This includes recording the nature of the fall, the circumstances leading up to the incident, and any contributing factors such as equipment malfunction or procedural lapses. For Nashville businesses, accurate and transparent incident reporting not only fulfills compliance obligations but also fosters trust within the workforce, assuring employees that their well-being is prioritized.
Post-incident analysis is an essential aspect of the fall protection compliance process. Reviewing incidents helps identify root causes and refine safety procedures to prevent recurrence, transforming each incident into an opportunity for improvement. Businesses should incorporate the findings into their training programs and site-specific plans, ensuring that lessons learned translate into practical changes on site. By systematically addressing incidents, Nashville companies strengthen their safety culture while aligning closely with both legal requirements and ethical responsibilities.
Conducting Regular Inspections and Audits
Regular inspections and audits are essential to maintaining an effective fall protection program, ensuring that all systems and processes remain functional and compliant with OSHA and TOSHA requirements. Inspections should include thorough checks of fall protection equipment such as harnesses, lanyards, and anchor points for signs of wear, damage, or improper configuration. By identifying and addressing deficiencies early, Nashville businesses can prevent accidents that might result from equipment failure while maintaining confidence in their fall protection measures.
Audits extend beyond equipment, examining the implementation and consistency of fall protection procedures across all active job sites. These evaluations should assess how effectively workers adhere to fall protection protocols, the adequacy of site-specific plans, and the condition of installed protective systems such as guardrails and safety nets. Audits can uncover procedural gaps, reveal patterns of non-compliance, and provide actionable insights for continuous improvement within a company’s safety culture.
Documentation plays a vital role during inspections and audits, providing a clear record that demonstrates due diligence and compliance to regulatory bodies during inspections or post-incident reviews. Maintaining a structured log of findings, corrective actions, and follow-ups reinforces a culture of accountability within the organization. Nashville businesses that prioritize regular inspections and audits as part of their fall protection programs reduce risk while building a proactive approach to safety that aligns with both operational goals and compliance obligations.
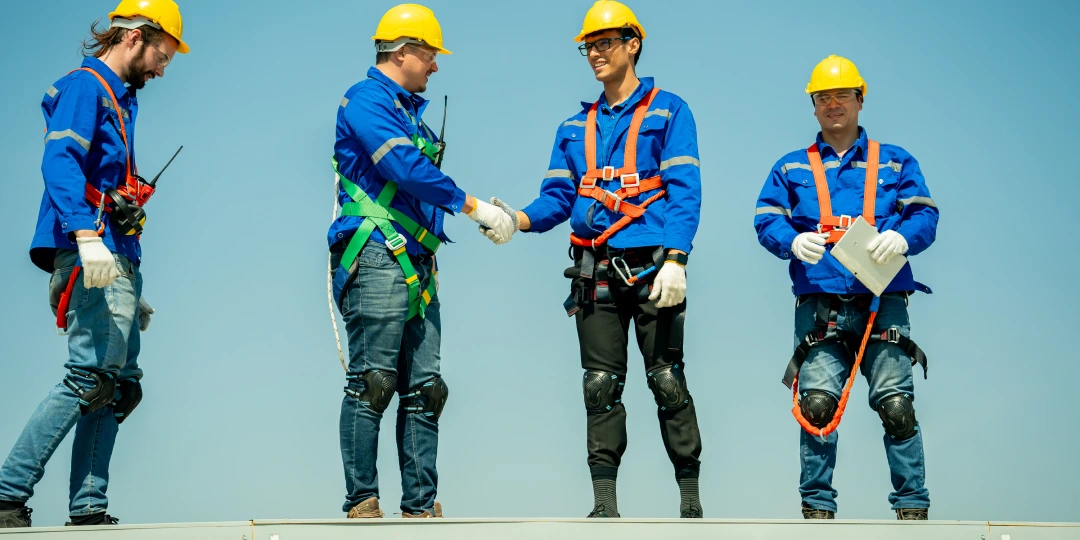
Frequently Asked Questions
1. What are the basic fall protection requirements for construction sites in Nashville?
OSHA requires fall protection for workers operating at heights of six feet or more on construction sites, with measures like guardrails, safety nets, and personal fall arrest systems. In Nashville, businesses must also follow TOSHA guidelines and may need to meet local codes depending on project type and location. A site-specific fall protection plan ensures you address these requirements while adapting to the unique conditions of each job site.
2. How often should fall protection equipment be inspected?
Fall protection equipment, including harnesses, lanyards, and anchor points, should be inspected before each use and undergo thorough periodic inspections according to manufacturer guidelines and OSHA standards. Regular inspections help identify wear or damage early, ensuring that the equipment remains reliable and compliant while protecting workers from potential failures on site.
3. Why is partnering with Fortier Loss Control beneficial for fall protection compliance?
Fortier Loss Control provides expert assessments, tailored training, and ongoing compliance support, helping Nashville businesses identify site-specific fall hazards and implement effective safety measures. Their expertise ensures fall protection programs meet OSHA and TOSHA requirements while fostering a safety-focused culture, reducing incident risks, and protecting your team and operations.
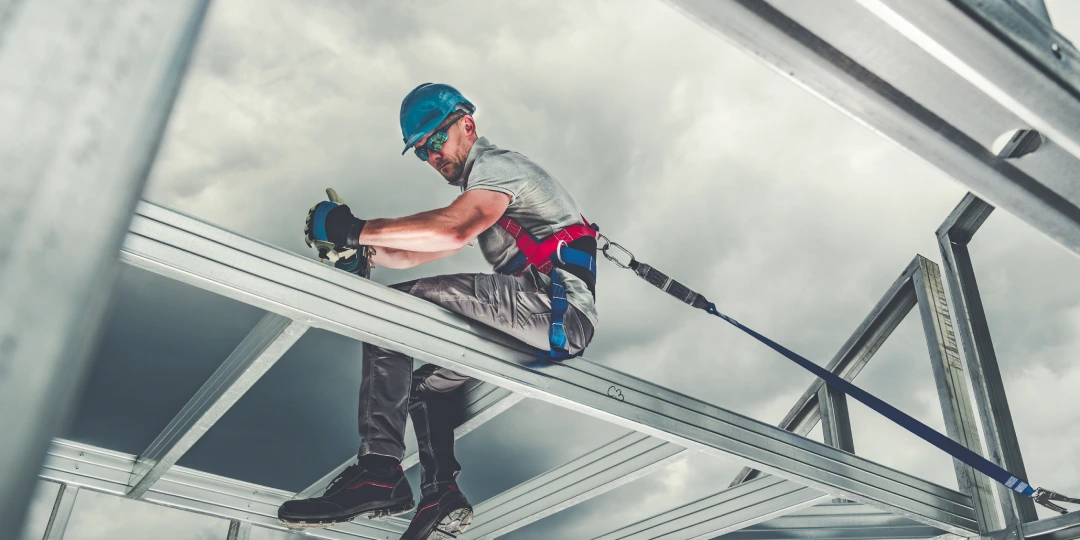
Conclusion: Prioritizing Safety While Staying Compliant
Fall protection is not simply a compliance checkbox; it is a proactive commitment to the well-being of workers and the stability of business operations in Nashville’s demanding construction and industrial sectors. By investing in fall protection measures, businesses demonstrate that the safety of their teams is not negotiable, fostering a culture where every employee feels valued and protected. This commitment resonates throughout the organization, creating a work environment where safety practices are not seen as a burden but as a shared responsibility that safeguards lives.
Compliance with OSHA, TOSHA, and Nashville-specific requirements ensures that fall protection programs are built on a strong legal and ethical foundation. Adhering to these standards protects businesses from costly fines, legal liabilities, and operational disruptions that can arise from non-compliance. It also positions organizations as reliable partners in the market, enhancing their ability to attract and retain skilled workers who prioritize safety-conscious employers. In an industry where reputational strength is a valuable asset, demonstrating a steadfast commitment to fall protection is a competitive advantage.
Partnering with Fortier Loss Control strengthens this commitment by providing the expertise, resources, and ongoing support necessary to build and sustain effective fall protection programs. Their tailored assessments, practical training, and compliance guidance equip Nashville businesses to stay ahead of regulatory changes while reducing risk across every project site. By prioritizing safety through consistent fall protection practices, businesses not only comply with regulations but also contribute to a safer, more productive workforce that drives long-term success and growth.